The Making of 'REMNANT 1'
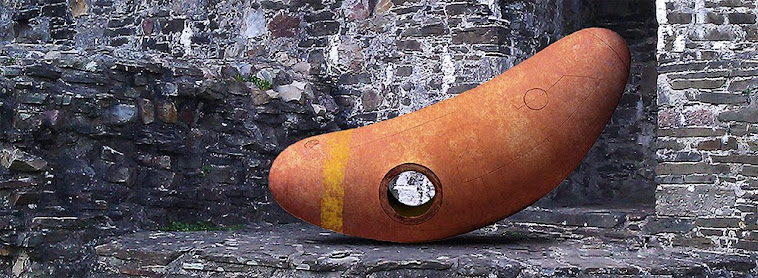
REMNANT 1
This blog is about how I produced the sculpture 'REMNANT 1'. I plan to document much of the process to allow people to see the amount of work that goes into a large outdoor piece of work.
TEMPLATE

Using the 'grid' method, I have scaled-up the original sketch to create this template, which I will use as a guide to make my armature.
ARMATURE

Using the template I have begun to cut chipboard to start the armature. I will need the armature to be able to produce a former.
Having cut out the central spine, I have now cut out circular ribs which will give the piece its shape.
To strengthen up the armature I have screwed in some struts between the ribs which help prevent any flex in the armature.
PLASTERING
The images above show the fleshing out process. I began by covering the armature with cling film until it was taught, then layers of scrim and plaster helped to build up the surface. Continuing to add plaster allowed me to start smoothing the surface, and by scraping and adding plaster I will be able to get a smooth surface all over.
PORTHOLES
As this piece is meant to resemble something mechanical I am adding portholes to either side of the former; I have made an mdf pattern to attach to the newly smoothed plaster form.
Above and below are images of how the pattern has been blended into the form using more plaster.
ADDING DETAILS
Above is an image of the finished plaster pattern with the details added to the surface. Below right is an image of the panel lines with round impressions to denote the placing of my bolts at a later stage.
The title of the piece is carved into one of the panels. Using a paper template I transfered the text to the plaster and then cut it out using a scalpel.
SAND MOULDS
The images above show how I went about creating the moulds for each individual panel on the former. This process was repeated for each of the 16 panels and each mould took between 8 and 10 hours. I first constructed a segmented wooden frame to fit onto my former and held it in place with screws; then I put cardboard around the edges. Kiln dried sand is mixed with Sodium silicate and then placed into the frame, ramming the sand between layers ensures a tightly packed sand mould. Using a steel spike, holes are pushed into the sand to allow CO2 gas to be pumped in, this reacts with the sodium silicate and hardens the sand. The section of the mould is removed from the former and a packing material (foam etc) is placed onto the surface. Keys are cut into the sand and the ramming and gassing process is repeated for the second half of the mould. The mould is opened and the packing material is removed, this leaves a cavity within the sand to receive metal later. The running system is carved into the sand and the face surface of the mould is treated with a mould wash that is set alight to harden and remove moisture. The 2 halves of the mould are glued together and strapped using metal banding.
Subscribe to:
Posts (Atom)